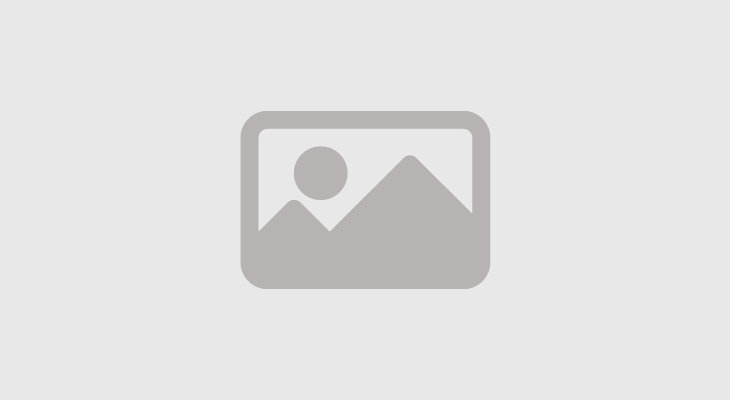
National Occupational Health and Safety Day: Employers need to change their attitude towards spending on worker health protection
Dr. Muhammad Mahtab Hossain Mazed
Today Sunday 28th April is International Occupational Health and Safety Day 2024. Since 2003, the International Labor Organization (ILO) and various countries around the world have been celebrating the day. This year, the day will be celebrated for the 8th time. Ministry of Labor and Employment.
After the Tazreen Fashion fire in 2012 and the Rana Plaza collapse on April 24, 2013, the issue of workplace safety for Bangladeshi workers became widely discussed. Since 2016, the day has been observed since 2016 with the aim of ensuring the occupational and health safety of workers injured or killed in workplace accidents in Bangladesh, mainly in memory of the Rana Plaza collapse.
> Objectives of occupational health and safety are-
a) Employees of all professions will be promoted by achieving physical, mental and social welfare.
b) Prevention of health risks to workers due to working environment.
c) protect the health of workers from harmful effects by protecting them from hazardous work or hazards;
d) Can create and manage the professional environment according to the physical and mental capabilities of the employees.
> Health awareness of workers
Health is the root of all happiness. If the employees of an organization are not physically fit, they cannot work attentively. As a result, errors are more likely to occur and absenteeism rates increase. As a result, both the workers and the owners are affected. Therefore, it is imperative for all the workers, administration and owners to be health conscious.
> Hygiene
Hygiene is a science that deals with the need for prevention and health awareness before we get sick. Personal health is the complete healthy life of a person's physical, mental, environmental and social conditions. Personal hygiene keeps others safe from getting sick just as it keeps us safe.
> Occupational diseases
All the diseases or disorders which a worker suffers or may develop while working due to the work environment and type of work are called occupational diseases. Some occupational diseases are mentioned below-
1. Skin disease 2. Respiratory diseases 3. Muscle and bone disorders 4. Hearing loss 5. Cancer 6. He and mental health problems 7. Infectious diseases
> Causes of occupational diseases
A worker or an employee may suffer from illness during work generally due to 3 reasons-
1. Regarding work environment: Chaos, loud noise, high temperature, lack of adequate ventilation, lack of adequate lighting and dust can cause a worker to suffer from various diseases. For example, loss of vision, loss of appetite, lung diseases, tuberculosis, inflammation of the airways, etc.
2. Personnel: Lack of necessary skills, lack of knowledge of guidelines, age and lack of physical ability can also cause various ailments.
3. Emotional Attrition: Behavior of superiors or colleagues at workplace, discrimination, job insecurity, excessive work pressure, long working hours, unnecessary harassment, torture etc. have an adverse effect on an employee which reduces his enthusiasm and motivation at work and makes him unable to adjust himself to work. creates obstacles.As a result, he gradually became mentally ill.
> Labor regulations in the field of health and safety
Every establishment shall be kept clean and free from noxious vapors arising from any sewer, sewage or other filth and in particular—
(a) The floors, workrooms, stairs, passageways of the establishment shall be swept and removed daily in covered boxes, so that the said garbage cannot spread odors or germs. Metallic materials, strong smelling wastes, chemical wastes and medical wastes should be removed regularly in different boxes on a daily basis.
(b) The floor of every workplace shall be washed with water at least once a week depending on the conditions and the nature of the work and, if necessary, disinfectants shall be used for washing. Depending on the situation, the floor should be washed with a wet cloth using a disinfectant.
(c) Where a floor becomes so wet due to the manufacturing process that it requires dewatering. In that case, water drainage is required, in that case, proper arrangement of water drainage should be made.
• The floor must be constructed of impermeable material.
• The construction of the said floor should be sloped and connected to the main drainage system of the factory through suitable drains, so that the drain water or any other liquids cannot accumulate on the floor.
(d) All internal walls, partitions, roofs, stairs, passageways of the establishment-
• If painted or varnished, at least once every three years
• To be repainted or varnished. painted or varnished and
• If the exterior is smooth, clean with water, brush and detergent at least once every fourteen months.
In other cases lime or paint should be done at least once every fourteen months.
(e) All records of the said proceedings shall be recorded in the prescribed register.
> Ventilation and temperature in the workplace
Every establishment should have adequate ventilation system for fresh air flow in every work room.
Every such room shall be kept at a tolerable level of temperature and every work room of every establishment shall have a sufficient number of reversible windows to facilitate the flow of fresh air. Provided, however, that where ventilators are not practicable, exhaust fans may be installed so that the workers can work in reasonable comfort, so as to prevent injury to the workers. Provided further that ventilation shall not be required if the workplace is air-conditioned. At least one thermometer (thermometer) shall be kept in working condition in every work room and it shall be of proper standard and shall be placed in a visible place on the wall of the work room. If necessary, the walls and ceiling of the room should be made in such a way that the temperature does not increase and should be kept as low as possible.
> Number of employees
• This kind of additional workers cannot be done simultaneously if the health of the workers working in any workplace of the organization is compromised.
• At least 9.5 cubic meters of space should be provided for each worker employed in each workshop (not to be taken into account if the height of any room is more than 4.25 meters from the floor).
• If the Chief Inspector requests an owner by order in writing, a notice board shall clearly state the maximum number of persons allowed to work in each workroom of the establishment.
The Chief Inspector may, by order in writing, permit the working premises of any establishment, if he is satisfied that the health of the workers employed therein does not require compliance with this provision.
> Lighting system
• In every part of an establishment, where workers work or travel, adequate, normal,
• Provide artificial or both lighting.
• Installation of all glass windows and roofs used to illuminate the workplaces of each institution
• Keep both sides of windows clean. In every institution- the diffused or reflected light from any transparent substance or lamp or
• Effective measures must be in place to prevent any form of shadowing that may cause strain on a worker's eyes or risk of injury.
> Provision of food and water
• Sufficient supply of fresh water for drinking of all workers employed in every establishment shall be provided at a convenient place and stored in a hygienic manner.
• Every water supply point should be clearly marked with the words 'drinking water' in Bengali.
• In all establishments where two hundred and fifty or more workers are generally employed, provision should be made to provide chilled drinking water during summer.
• Oral rehydration therapy should be administered to workers who become dehydrated due to working near excessive heat generating equipment.
> Toilets and washrooms
Every establishment shall have the required number of sanitary toilets and washrooms at convenient locations for easy use by the working workers during working hours.
• The said toilets and changing rooms shall be provided separately for male and female workers.
Toilets and washrooms shall be provided separately for male and female workers.
The use of disinfectants and cleaners at the owner's own expense in the said toilets and washrooms
The medium should always be kept clean and hygienic.
> Litter box
For every 100 workers in each establishment:
A separate garbage and pick-up box should be kept;
The pikdani should be filled with sand and topped with bleaching powder;
Garbage box should be made of plastic and with a lid, the accumulated garbage should be removed daily and both areas should be cleaned with disinfectant;
The dustbin and garbage box shall be placed near the door of the workshop and so on
should be placed so as not to spread bad smell and garbage;
No person shall spit or litter in any establishment other than slops and litter boxes and a notice of this provision shall be posted in a suitable place within the establishment in a manner easily visible.
> Occupational safety
Working safely by preventing any adverse conditions is called occupational safety.
There are three types of occupational safety namely-
1. Personal security
Personal Safety In industries workers use personal safety equipment to ensure personal safety as all precautions are followed to protect oneself from accidents.
2. Safety of machinery and equipment
After completing the work without causing any damage to the equipment, it should be closed and cleaned. Then properly stored, this efficiency ensures the safety of machinery and equipment.
3. Safety procedures for machinery and equipment:
• Proper operation of the machine; The machine must be turned off after work;
• Keeping the work area clean and tidy;
• Immediate shutdown of the machine and prompt repair in case of any disturbance;
• Occasional checking of electrical connections etc.
3. Factory safety
Protecting the workshop from all kinds of accidents is called workshop safety. For example-
• keeping all electrical connections insulated with necessary protective devices;
• Avoid welding and grinding near combustible materials;
• Provision of fire fighting materials, water, sand and fire extinguishers;
• Promptly report to the fire station in case of accidental fire; Keeping factory interior and exterior clean at all times.
> Personal protective equipment
Personal Protective Equipment (PPE): Personal protective equipment or PPE is the personal protective equipment or clothing that is used to protect the worker from the risk of accidents at work. Personal protective equipment (PPE) can be classified as follows on the basis of which parts of a person are to be protected from possible harm or accident:
1. Jain
Aprons are used to protect factory workers from extreme temperatures, bad weather, spilled chemicals or industrial fragments, high velocity air currents, sharp objects entering the body and dust etc. Aprons are of different types for different situations, such as boiler suit, chemical suit, dent, ag full body cover suit, jacket etc. Wearing proper apron while working in the workshop protects clothes and body from dust, sand, various types of lubricants, metal chips, sparks and splinters.
2. Hand gloves
Hand gloves are used to protect hands from high temperatures, sharp objects, heavy objects, electric shocks, chemicals, skin irritants, etc.
3. Safety shoes
Safety shoes, safety boots, leggings (leg coverings made of thick fabric), pats (thin coverings) to protect the feet from slippery floors, wet floors, sharp objects, falling objects, chemical spills and other liquids etc. in the workshop or workplace. etc. are used. Safety sweats or safety shoes protect Wenkar/Karma from injury from heavy metals, hot molten metal, and falling objects. It also protects the weatherman or worker from electric shock.
4. Safety mask
Many times in the workshop, it is difficult to breathe when there is smoke, toxic gas, stench etc. In such conditions, gas mask must be used for breathing safety when working in the workshop. Sometimes oxygen mask is also used when the oxygen level is low in Ravas. To protect against germs, doctors and medical staff in hospitals wear three-layer cloth masks, surgical masks and N-15 masks.
5. Ear plugs or ear protectors
Noise pollution at work can cause ear damage if the noise level is more than 85 decibels. Using ear muffs, ear defenders, ear plugs to prevent any kind of high level noise in the workshop protects hearing aids and ears.
6. Safety goggles or eye protection equipment
There is a possibility of damage to the eyes if chemical substances or metal objects, dust, catalyst powder, gas, steam and radiation, harmful light rays emitted during welding directly enter the eyes during the workshop. Therefore, the workshop workers should wear PPE for eyes such as safety glasses, pulse, face shield, vending helmet etc. to avoid these damages. Safety goggles must be used while grinding, drilling, turning, boring, winding etc. in the workshop.
> Training:-
An employer is obliged to provide practical and relevant training on health and safety to his subordinates and to ensure a safe and healthy environment for workers at work. An employer should raise awareness among workers by providing on-the-job training. There is a risk of bodily injury, poisoning or serious illness with this type of dangerous operation
In that case, it is under the responsibility of the employer to provide periodical medical care to the worker engaged in the operation and to debar him if he is not proved fit for work. Workers engaged in this type of operation and work on dangerous machines must be adequately trained and supervised.
And according to the provisions of the Department of Inspection of Factories and Institutions, it is mandatory to form a safety committee in factories or industrial establishments where 50 or more workers are employed. But most of the factories are not complying with these provisions of the law, due to which the loss of life in accidents is increasing.
There are checklists for factory construction. According to the checklist, there are several tasks and rules to be followed both internally and externally in the factory. In this case, there are some things before the start of the factory, some things have to be done while the factory is running or in operation. It depends on the type and condition of the factory. Such as trade license for setting up factory, factory layout plan, environmental clearance, proper authority approval, communication system, own fire fighting system, road for fire service vehicles, required generator, power management, sewage and waste management, access of workers etcHow many pre-conditions have to be followed by the employers including exiting Labor Act 2015 and rulesIn addition to establishing these factories properly, the supervision and effective inspection of appropriate authorities including the Directorate of Factories and Institutions Inspection (DIFE), Fire Service and Bangladesh Investment Development Authority (BIDA) can protect the sustainable environment of the factory and avoid various accidents including fire and explosion.
The existing condition of fire and other accident prevention should be reviewed in the light of inspection by identifying the structural weaknesses of industrial and commercial establishments. Specific steps should be taken to ensure a safe working environment in the factory. If this is not done, our image in the outside world will remain negative. Government policy support and supervision should be strengthened to remove barriers to all factories and their environment in view of the vast potential in the seamless export of our leather exports, agricultural processed products, shoes and bicycles to foreign countries.
Finally, we all need to remember – work for life, not life for work.
A change in the owner's attitude towards security expenditure is required. Keep in mind that security costs are essentially capital costs or investments. It is never an extra cost or a waste. A safe working environment not only saves workers' lives but also increases productivity. As a result, any cost or investment for the security of the organization, in the long run, is a benefit to the industry. It is everyone's hope that the state and employers will be able to understand this matter properly on the International Occupational and Health Safety Day.
The writer is a columnist and researcher Founder Chairman,Jatiya Rogi Kallyan Society
Comment / Reply From
You May Also Like
Latest News
Vote / Poll
ফিলিস্তিনের গাজায় ইসরায়েলি বাহিনীর নির্বিচার হামলা বন্ধ করতে জাতিসংঘসহ আন্তর্জাতিক সম্প্রদায়ের উদ্যোগ যথেষ্ট বলে মনে করেন কি?